From Nut to Mat - How Coir Matting is Made
Door mats might not stand out as being the most obvious product to boast an interesting manufacturing history, but the truth of the matter is that coir...
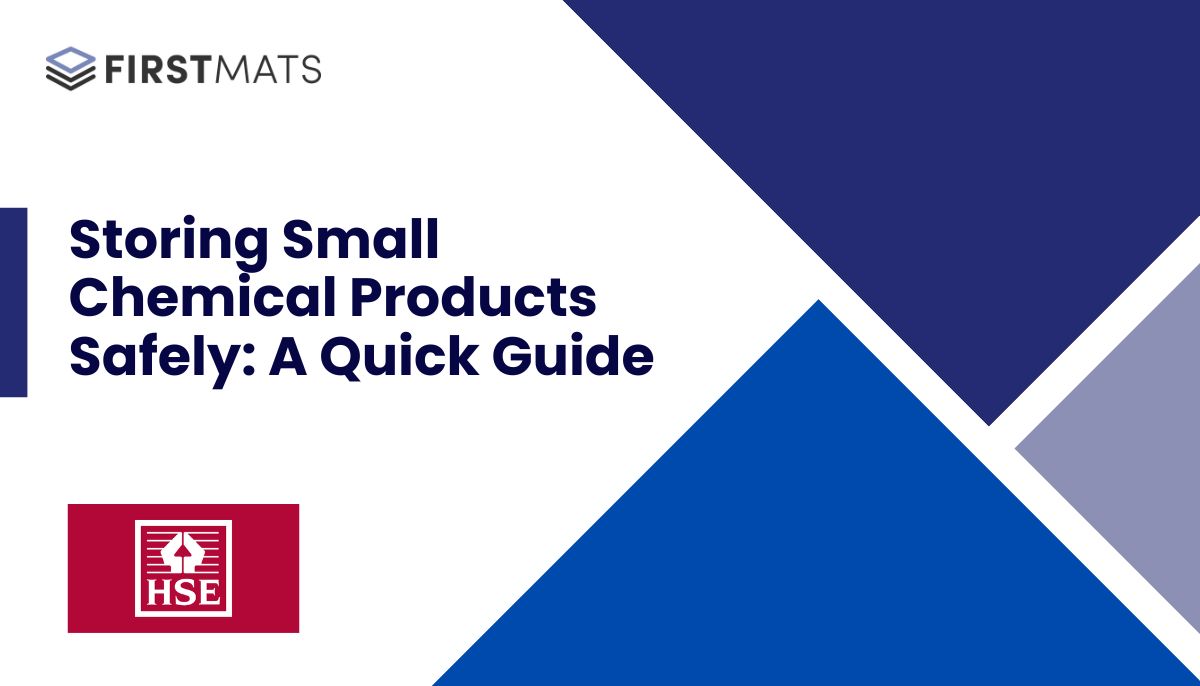
A Quick Guide to Storing Small Chemical Products Safely
Introduction This blog post provides a simplified guide to the Health and Safety Executive (HSE) document titled 'Storing Chemical SR24 Products (small scale)'....

Executive Summary of HSE Work-Related MSDs Statistics
Executive Summary: Work-Related Musculoskeletal Disorders Statistics in Great Britain This article provides a comprehensive summary of the key findings from the Health and Safety Executive (HSE) report on work-related musculoskeletal...
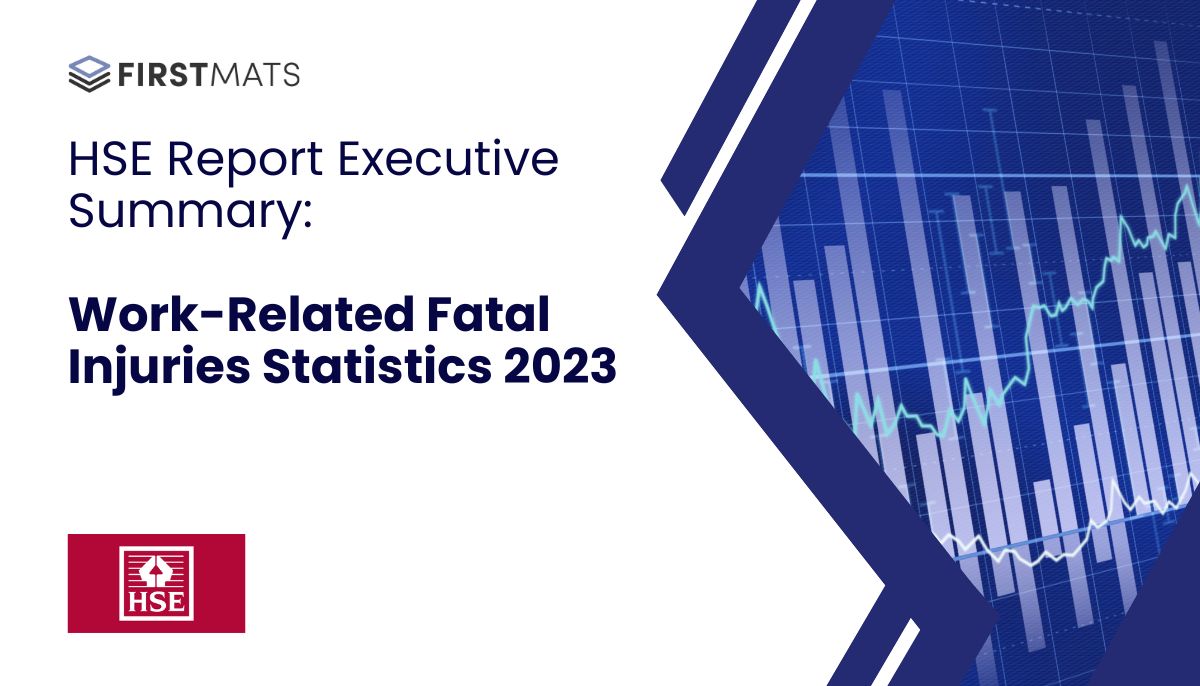
Executive Summary of HSE Work-Related Fatal Injuries Statistics
Executive Summary of HSE Work-Related Fatal Injuries Statistics This article is compiled by First Mats and provides an executive summary of the

The Costs to Britain of Workplace Accidents, Injuries and Ill-Health: HSE Report Summary
An Executive Summary of the HSE Report: Costs to Britain of Workplace Fatalities and Self-reported Injuries and Ill Health Published in November 2023, this report presents the latest estimates of...
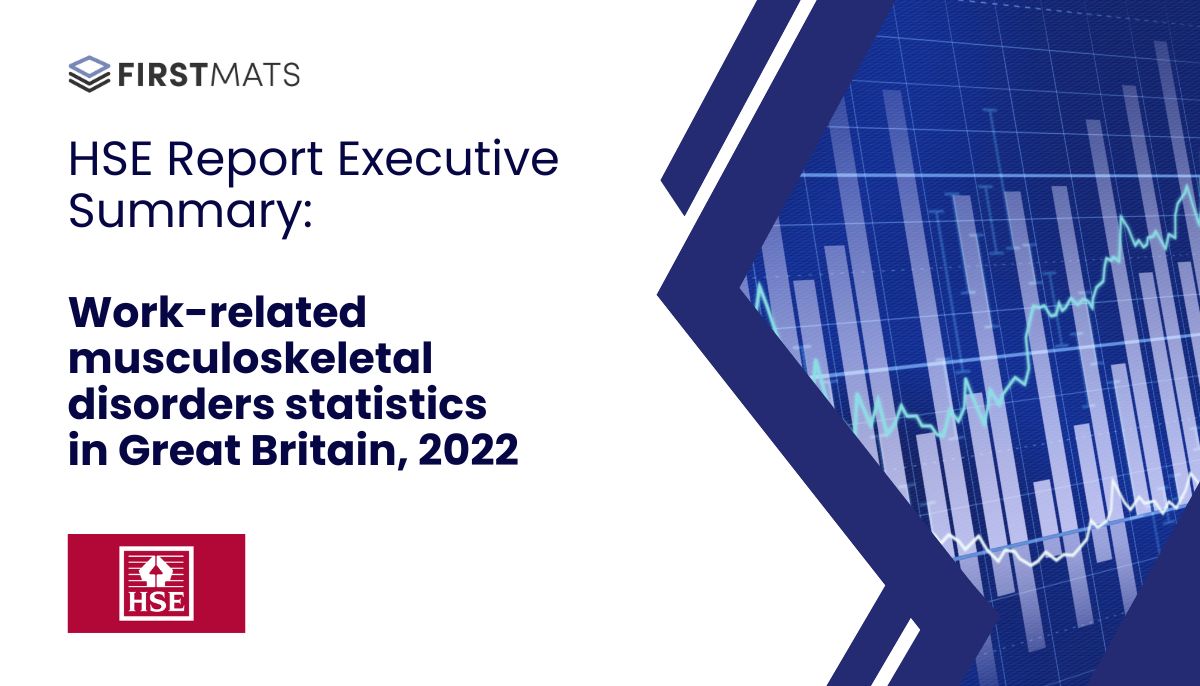
Summary of HSE Work-related Musculoskeletal Disorders Statistics 2022
Executive Summary of HSE Report 2022: Key Findings on Work-related Musculoskeletal Disorders This blog post provides a summary of the key findings from the Health and Safety Executive's (HSE) report...
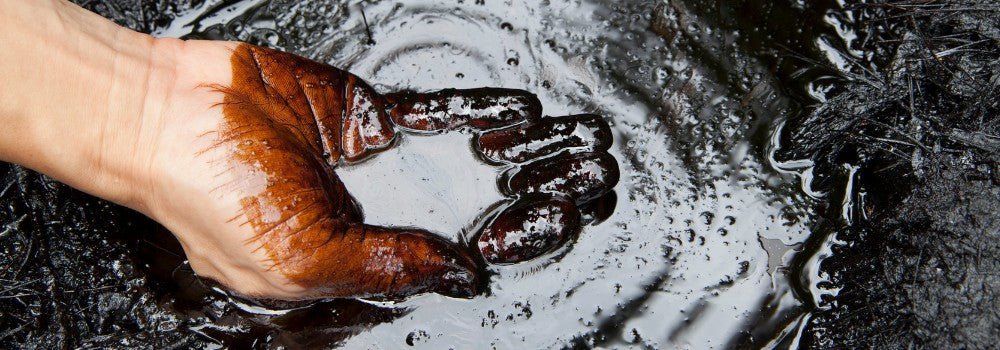
The Environmental Impact of Generator Spills and How to Mitigate Them
Generators, while vital in modern life for a variety of applications, come with certain environmental risks. When not managed properly, spills from these machines can have devastating effects on our...

How to Prevent and Clean Oil Spills in the Workplace: A Comprehensive Guide
Workplace oil spills are more than just an inconvenient mess; they present serious risks to employee safety and the environment. Several pieces of legislation in the UK, such as the...

AdBlue: Its Risks to Health and the Environment
In an era where environmental responsibility and sustainable practices take centre stage, understanding the various components of these efforts is paramount. One such component, extensively used in the automotive industry,...

The Best Colour Door Mats for People With Dementia
Dementia is a syndrome associated with an ongoing decline of brain functioning, affecting memory, thinking speed, language, understanding, judgement, mood, and movement. It impacts more than 850,000 people in the...

Tips for Moving Plasterboard Safely and Efficiently
Plasterboard, also known as drywall, is a common material used in construction and renovation projects. While it's a versatile and useful material, moving plasterboard can be challenging due to its...

Understanding UDL: Uniformally Distributed Load
What Does UDL Mean? UDL, or Uniformally Distributed Load, is a term used in the field of manual handling equipment to describe the weight capacity of a particular piece of...

Bund Integrity Testing - What You Need to Know
As a responsible business owner, protecting your assets should be one of your top priorities. One approach to securing your assets is using portable bunding solutions, such as

The Complete Guide to Foam Impact Protectors: Enhancing Workplace Safety
Impact Protection Foam is a vital component in industrial environments, serving as a crucial safeguard against injuries caused by impacts with hard surfaces. Designed with a...

Rising Stress Levels in the UK and the Impact on Workers - Facts and Statistics
A recent study conducted by First Mats has highlighted the growing issue of stress among the UK population. Our survey of over 1,000 UK adults found that more...

Mats for Wudu / Ablution Areas in Mosques
Here at First Mats, we have an extensive selection of wet room matting ideal for Wudu/ Ablution areas in Mosques and other spiritual sites. The outstanding water drainage, anti-slip...

The Most Unsafe Places to Work in Britain (2023)
The Health and Safety Executive releases updated figures on workplace injuries and fatalities annually, and its latest report has...

Workplace Safety Facts and Statistics
Workplace-related injury is shockingly high in the UK. And statistics from the Health & Safety Executive (HSE) show that thousands of UK workers are injured or killed on the...

A Simple Guide to ISO 14001 Certification
ISO 14001 certification is a globally recognised standard for implementing an effective environmental management system. It is designed to help organisations reduce their environmental impact, manage resources more efficiently, and...

How to Remove The Smell from Rubber Mats
Rubber mats are versatile and extremely useful in various applications, from gyms to warehouses to garage floors. They are naturally durable, flexible and have a long lifespan. However, amongst all...

Flyball - The Everything Guide
Are you looking for a new activity to enjoy with your dog? Perhaps you want to help socialise your pup while providing excellent exercise that stimulates their brain, agility, and...
From Nut to Mat - How Coir Matting is Made
Door mats might not stand out as being the most obvious product to boast an interesting manufacturing history, but the truth of the matter is that coir...
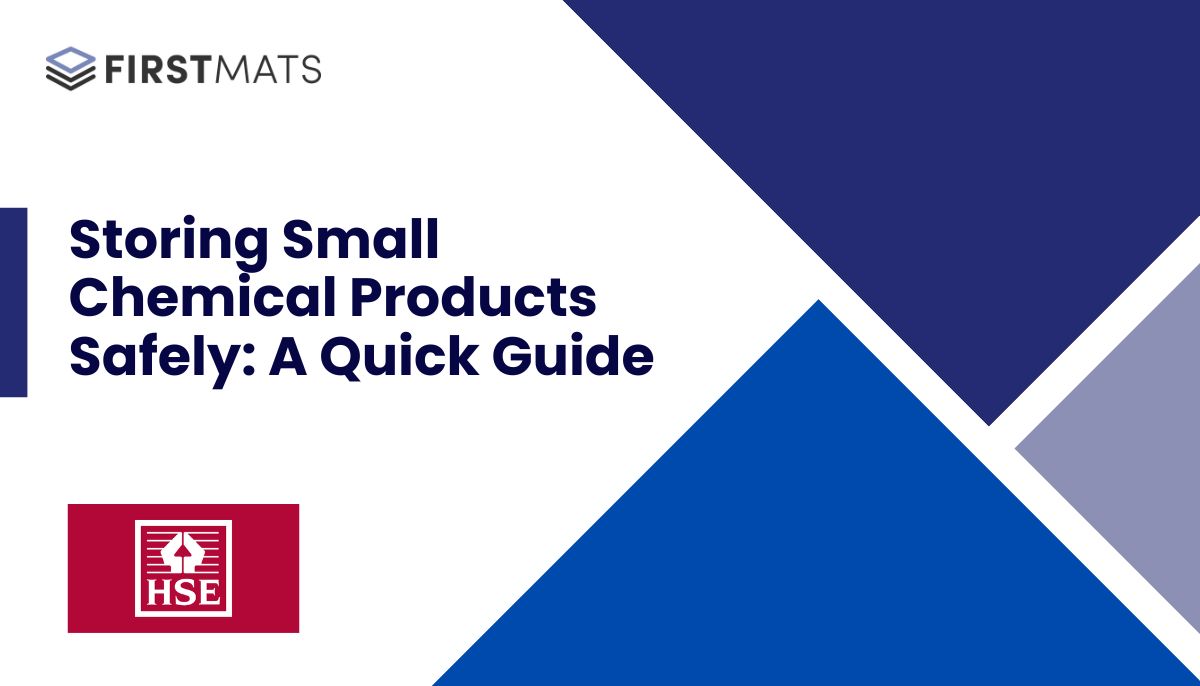
A Quick Guide to Storing Small Chemical Products Safely
Introduction This blog post provides a simplified guide to the Health and Safety Executive (HSE) document titled 'Storing Chemical SR24 Products (small scale)'....

Executive Summary of HSE Work-Related MSDs Statistics
Executive Summary: Work-Related Musculoskeletal Disorders Statistics in Great Britain This article provides a comprehensive summary of the key findings from the Health and Safety Executive (HSE) report on work-related musculoskeletal...
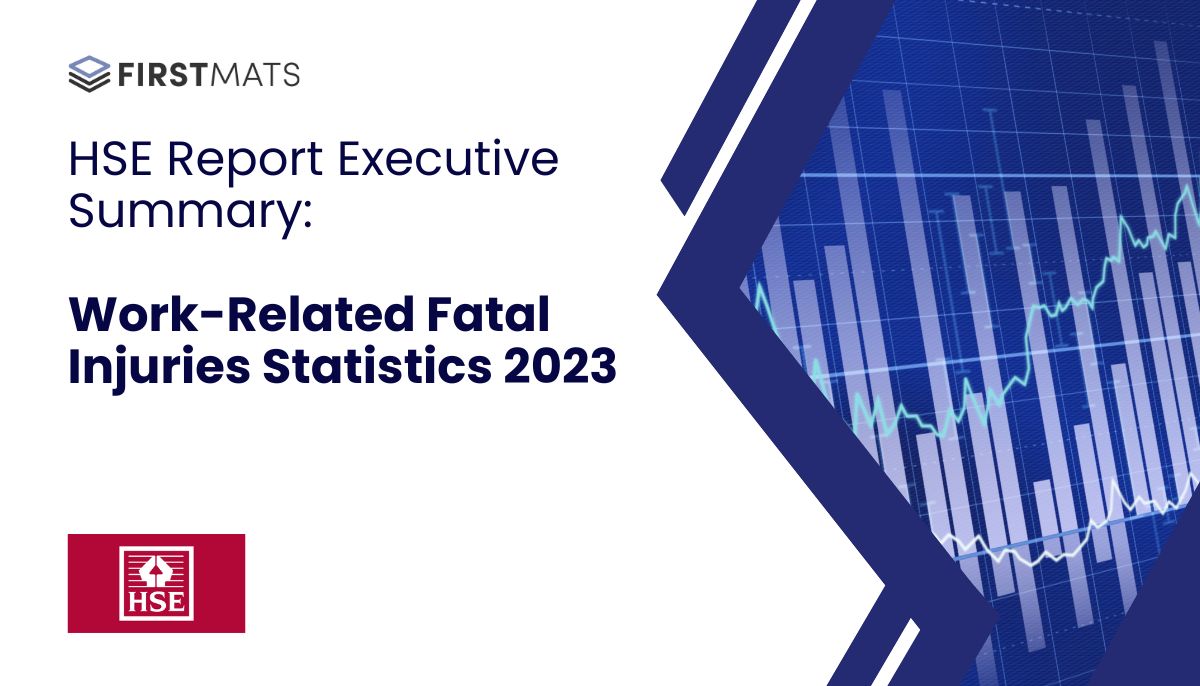
Executive Summary of HSE Work-Related Fatal Injuries Statistics
Executive Summary of HSE Work-Related Fatal Injuries Statistics This article is compiled by First Mats and provides an executive summary of the

The Costs to Britain of Workplace Accidents, Injuries and Ill-Health: HSE Report Summary
An Executive Summary of the HSE Report: Costs to Britain of Workplace Fatalities and Self-reported Injuries and Ill Health Published in November 2023, this report presents the latest estimates of...
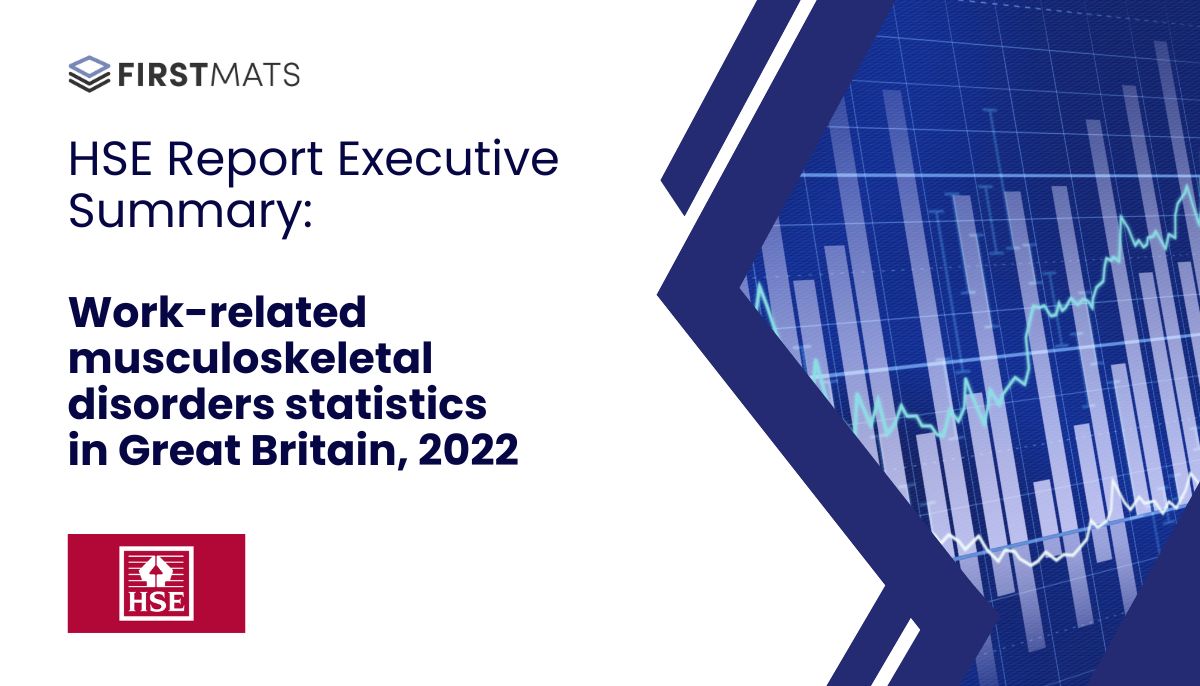
Summary of HSE Work-related Musculoskeletal Disorders Statistics 2022
Executive Summary of HSE Report 2022: Key Findings on Work-related Musculoskeletal Disorders This blog post provides a summary of the key findings from the Health and Safety Executive's (HSE) report...
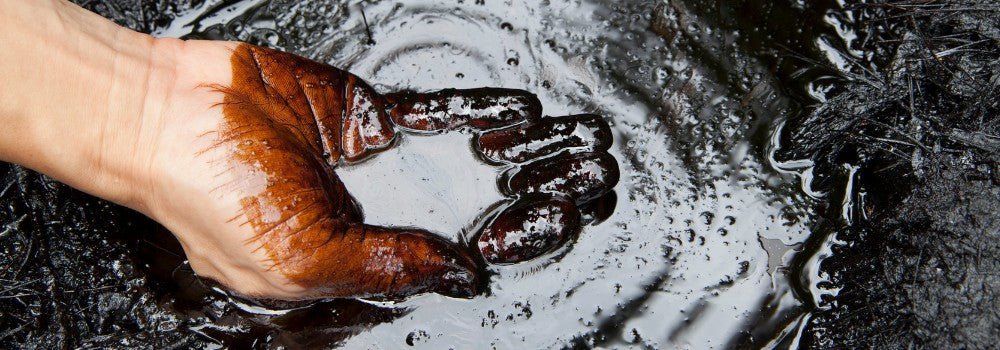
The Environmental Impact of Generator Spills and How to Mitigate Them
Generators, while vital in modern life for a variety of applications, come with certain environmental risks. When not managed properly, spills from these machines can have devastating effects on our...

How to Prevent and Clean Oil Spills in the Workplace: A Comprehensive Guide
Workplace oil spills are more than just an inconvenient mess; they present serious risks to employee safety and the environment. Several pieces of legislation in the UK, such as the...

AdBlue: Its Risks to Health and the Environment
In an era where environmental responsibility and sustainable practices take centre stage, understanding the various components of these efforts is paramount. One such component, extensively used in the automotive industry,...

The Best Colour Door Mats for People With Dementia
Dementia is a syndrome associated with an ongoing decline of brain functioning, affecting memory, thinking speed, language, understanding, judgement, mood, and movement. It impacts more than 850,000 people in the...

Tips for Moving Plasterboard Safely and Efficiently
Plasterboard, also known as drywall, is a common material used in construction and renovation projects. While it's a versatile and useful material, moving plasterboard can be challenging due to its...

Understanding UDL: Uniformally Distributed Load
What Does UDL Mean? UDL, or Uniformally Distributed Load, is a term used in the field of manual handling equipment to describe the weight capacity of a particular piece of...

Bund Integrity Testing - What You Need to Know
As a responsible business owner, protecting your assets should be one of your top priorities. One approach to securing your assets is using portable bunding solutions, such as

The Complete Guide to Foam Impact Protectors: Enhancing Workplace Safety
Impact Protection Foam is a vital component in industrial environments, serving as a crucial safeguard against injuries caused by impacts with hard surfaces. Designed with a...

Rising Stress Levels in the UK and the Impact on Workers - Facts and Statistics
A recent study conducted by First Mats has highlighted the growing issue of stress among the UK population. Our survey of over 1,000 UK adults found that more...

Mats for Wudu / Ablution Areas in Mosques
Here at First Mats, we have an extensive selection of wet room matting ideal for Wudu/ Ablution areas in Mosques and other spiritual sites. The outstanding water drainage, anti-slip...

The Most Unsafe Places to Work in Britain (2023)
The Health and Safety Executive releases updated figures on workplace injuries and fatalities annually, and its latest report has...

Workplace Safety Facts and Statistics
Workplace-related injury is shockingly high in the UK. And statistics from the Health & Safety Executive (HSE) show that thousands of UK workers are injured or killed on the...

A Simple Guide to ISO 14001 Certification
ISO 14001 certification is a globally recognised standard for implementing an effective environmental management system. It is designed to help organisations reduce their environmental impact, manage resources more efficiently, and...

How to Remove The Smell from Rubber Mats
Rubber mats are versatile and extremely useful in various applications, from gyms to warehouses to garage floors. They are naturally durable, flexible and have a long lifespan. However, amongst all...

Flyball - The Everything Guide
Are you looking for a new activity to enjoy with your dog? Perhaps you want to help socialise your pup while providing excellent exercise that stimulates their brain, agility, and...
Frequently Asked Questions
If you have any questions, we’re here to help
How long does delivery take?
Each product comes with a specified lead time for delivery. We'll keep you informed if there are any delays in meeting this timeline.
Typically, once you’ve finalised your order and approved the proof, it will take 4-5 business days to make and deliver your finished mat.
If my order is damaged, can I return or exchange it?
Got a problem with your order? If something's not right or you're not thrilled with the quality, just let us know within 14 days of getting it. Drop us a line, and we'll tell you what to do next—usually, it starts with you sending us a photo of the issue. Once we check that out, we'll sort you out with a refund or a new item, no fuss.
Can I get my mat delivered more quickly?
Need your item in a hurry? Just Contact us to explore the faster delivery options we might have for you!
If my custom mat is damaged, can I return or exchange it?
Got a problem with your order? If something's not right or you're not thrilled with the quality, just let us know within 14 days of getting it. Drop us a line, and we'll tell you what to do next—usually, it starts with you sending us a photo of the issue. Once we check that out, we'll sort you out with a refund or a new item, no fuss.