
Portable Containment Bund - Compatibility Chart
Selecting suitable equipment for chemical storage and spill control depends on verified material compatibility. This guide summarises how common substances interact with PVC with a protective proofing layer (PES/PVC), enabling...

Colorful Classrooms: Leveraging Floor Matting and Adjustable Furniture to Create Engaging Spaces
Learning environments are evolving to meet the needs of students who think, move, and learn differently. Colourful classroom spaces that combine thoughtful design with vibrant visual elements are more than...

Entrance Mat Sizing Guide
Have you ever purchased a mat only to find it's too small to catch dirt or too large for your doorway? Selecting the right-sized mat is essential, not just for...

What Are the Most Eco-Friendly Floor Mats?
Have you ever paused at your front door and wondered if your doormat is eco-friendly? We often focus on recycling and reducing energy use in our homes, but even a...

Which Floor Mats Can You Use Outdoors?
Have you ever stepped outside your door and slipped on a wet, ineffective mat? Or perhaps you've noticed your once-attractive mat has deteriorated rapidly after being exposed to rain and...

How to Fit a Recessed Door Mat
Recessed door mats keep your entryway tidy and safe by fitting flush with your floor. If you have an existing matwell or frame, installing coir...

Why Branded Floor Mats Are a Smart Business Investment
Have you ever considered the importance of your entrance area to your overall business image? Are you making the most of every opportunity to showcase your brand?...

5 Benefits of Using Cable Protectors
Cable protectors are a great way to ensure your cables stay safe and in place. They can be used for many everyday purposes, such as preventing tripping hazards, covering unsightly...
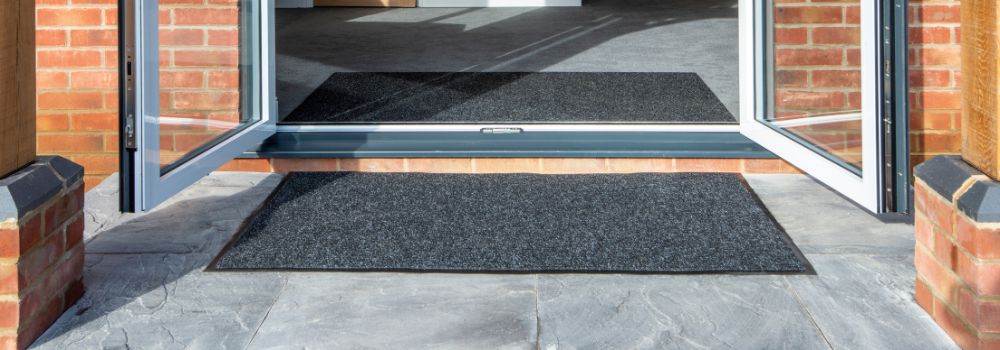
Boost Your Home’s Curb Appeal with the Right Doormat
Have you ever walked up to a house and immediately felt like this is a house you want to own, even before even stepping inside? That first impression is...

The Versatility of Floor Mats: More Than Just the Front Door
When most people think of floor mats, the front door is the first place that comes to mind. While it’s true that entrance mats are essential...
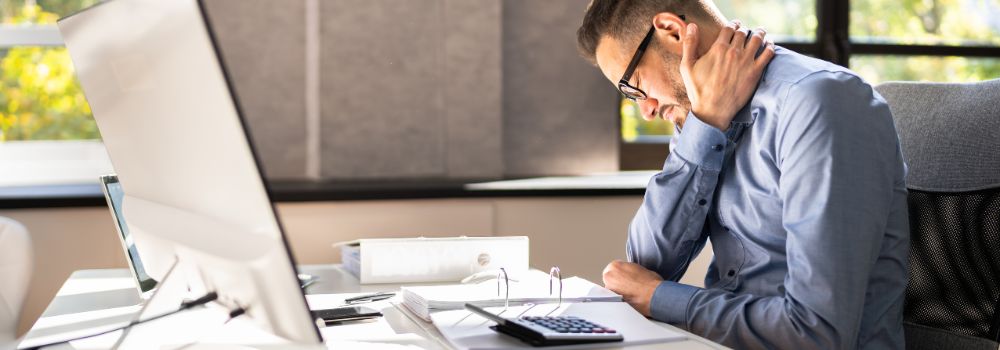
Ergonomic Workstations: Things You Need to Know When Setting One Up
Creating an ergonomic workstation is essential for maintaining employee well-being, increasing productivity, and improving staff retention. Poorly designed workstations can lead to discomfort, musculoskeletal issues, and decreased efficiency. This guide...

How to Protect Your Hardwood Floors Using Entrance Mats
Hardwood floors add warmth and elegance to any home, but keeping them looking pristine requires careful maintenance. One of the biggest threats to hardwood flooring is the dirt and grime...
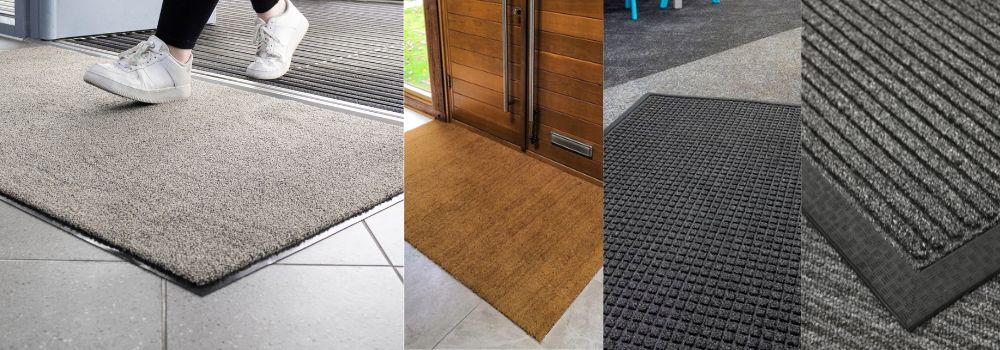
The Different Textures of Entrance Matting and Their Benefits
Entrance mats may seem like a simple addition to your home or business, but not all mats are the same. A mat's texture is crucial in how well it...

What Vegans Need to Know About Door Mats
This article has been written by our Director, Richard O’Connor, who has been exploring how well door mats can align with vegan values. As a vegetarian making more vegan choices...
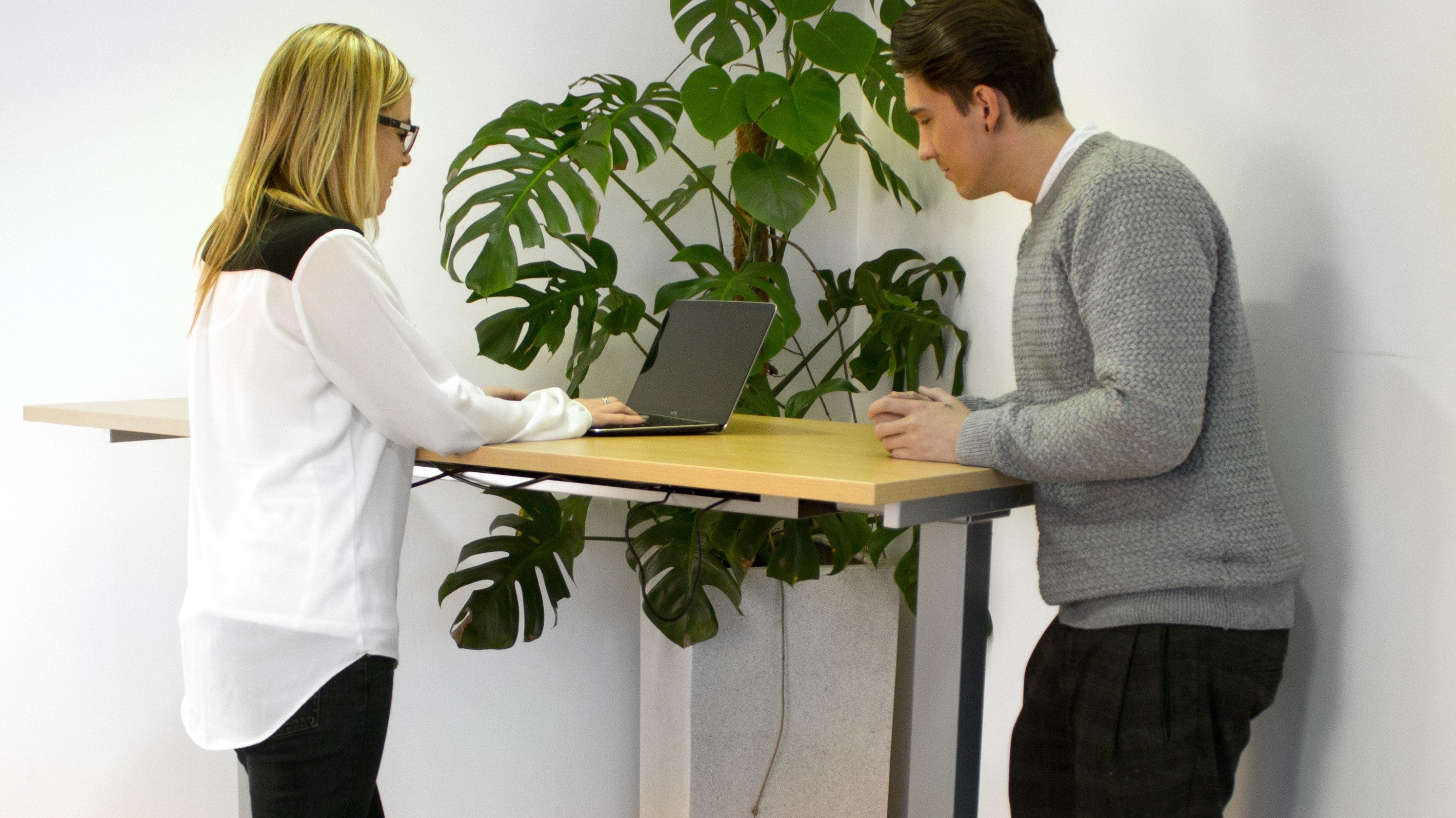
6 Tips for using a Standing Desk Correctly
As people are becoming more aware of their fitness levels and ways in which they can stay healthy, standing desks have increased in popularity because those who have previously had...

5 Creative Ways to Use Your Logo on Products to Boost Brand Awareness
Businesses today compete for attention across countless platforms. Customers have more choices than ever, so brand loyalty is becoming harder to secure. In this landscape, a brand’s image needs to...

The Different Surfaces of Anti-Fatigue Matting Explained
Understanding the different surface textures of anti-fatigue matting is essential for selecting the right one for your workspace. Anti-fatigue mats come in various textures, each designed to provide specific benefits...

Industrial Matting Fact Sheet
Introduction Industrial matting plays a crucial role in maintaining safety, comfort, and efficiency in various work environments. This fact sheet provides essential information about the different types of industrial mats,...

How to keep warm at work: Cost-effective ways to beat the bills
Are you concerned about your business running costs now that energy prices have gone through the roof? Electricity prices have increased 74% for large industrial units in the past...

The Cost of Slips, Trips, and Falls to British Industry
The Cost of Slips, Trips, and Falls to British Industry Are slips, trips, and falls costing your business dearly? Is your workforce underperforming? Are you missing expertise on the floor...

4-Day Work Week in the UK - Key Facts & Statistics
The world of work has seen a lot of change since the beginning of the 2020s, and — in turn — many companies have placed employee well-being at the top...
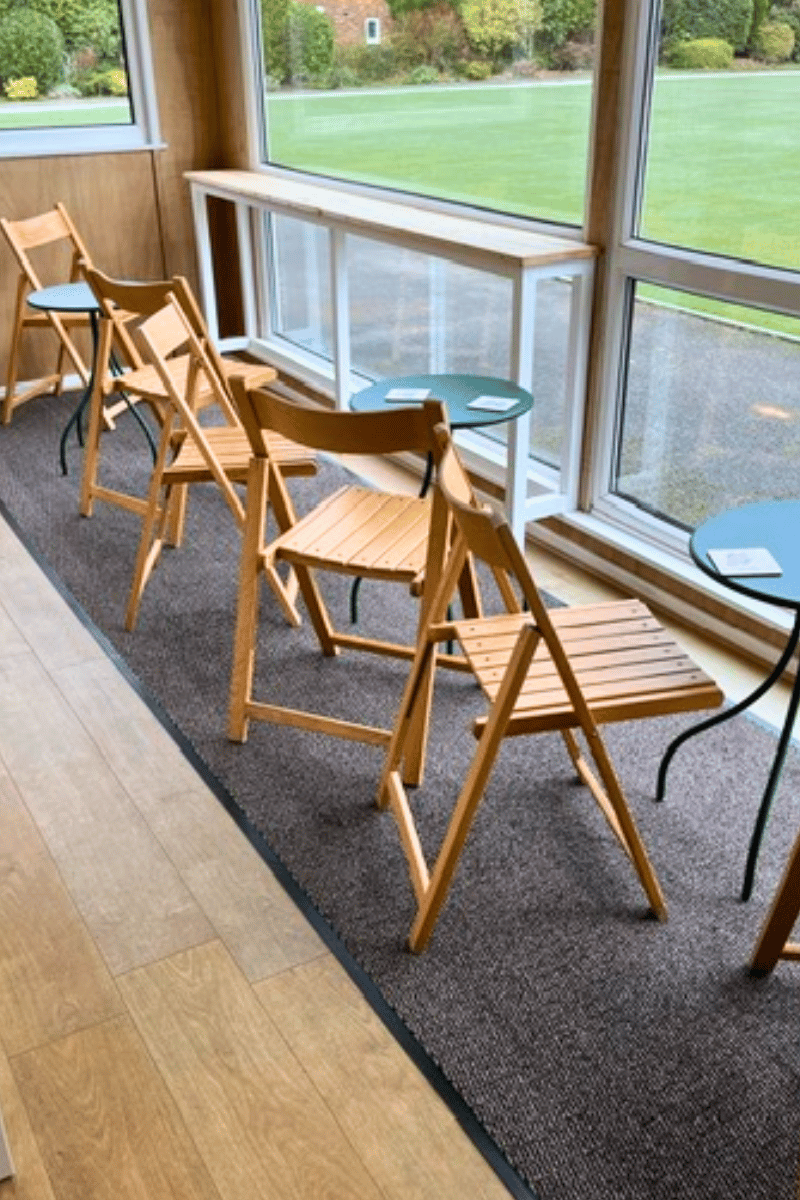
Prestbury Bowling Club Refurbishment
Problem When Christine was assigned to refurbish Prestbury Bowling Club, her main objective was to maintain a safe and welcoming...

Portable Containment Bund - Compatibility Chart
Selecting suitable equipment for chemical storage and spill control depends on verified material compatibility. This guide summarises how common substances interact with PVC with a protective proofing layer (PES/PVC), enabling...

Colorful Classrooms: Leveraging Floor Matting and Adjustable Furniture to Create Engaging Spaces
Learning environments are evolving to meet the needs of students who think, move, and learn differently. Colourful classroom spaces that combine thoughtful design with vibrant visual elements are more than...

Entrance Mat Sizing Guide
Have you ever purchased a mat only to find it's too small to catch dirt or too large for your doorway? Selecting the right-sized mat is essential, not just for...

What Are the Most Eco-Friendly Floor Mats?
Have you ever paused at your front door and wondered if your doormat is eco-friendly? We often focus on recycling and reducing energy use in our homes, but even a...

Which Floor Mats Can You Use Outdoors?
Have you ever stepped outside your door and slipped on a wet, ineffective mat? Or perhaps you've noticed your once-attractive mat has deteriorated rapidly after being exposed to rain and...

How to Fit a Recessed Door Mat
Recessed door mats keep your entryway tidy and safe by fitting flush with your floor. If you have an existing matwell or frame, installing coir...

Why Branded Floor Mats Are a Smart Business Investment
Have you ever considered the importance of your entrance area to your overall business image? Are you making the most of every opportunity to showcase your brand?...

5 Benefits of Using Cable Protectors
Cable protectors are a great way to ensure your cables stay safe and in place. They can be used for many everyday purposes, such as preventing tripping hazards, covering unsightly...
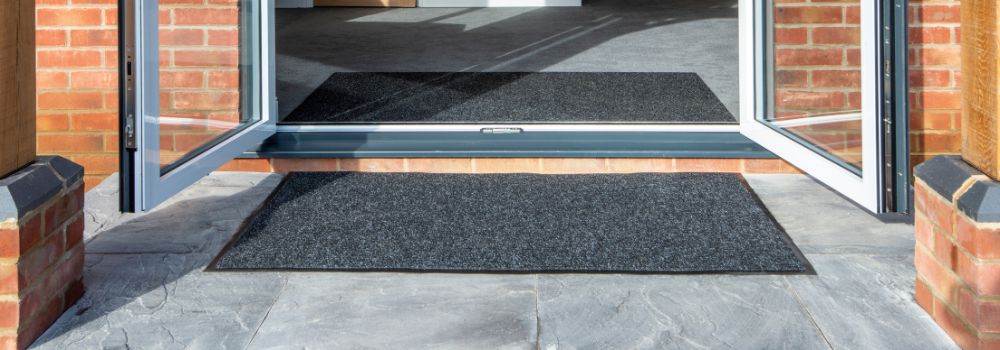
Boost Your Home’s Curb Appeal with the Right Doormat
Have you ever walked up to a house and immediately felt like this is a house you want to own, even before even stepping inside? That first impression is...

The Versatility of Floor Mats: More Than Just the Front Door
When most people think of floor mats, the front door is the first place that comes to mind. While it’s true that entrance mats are essential...
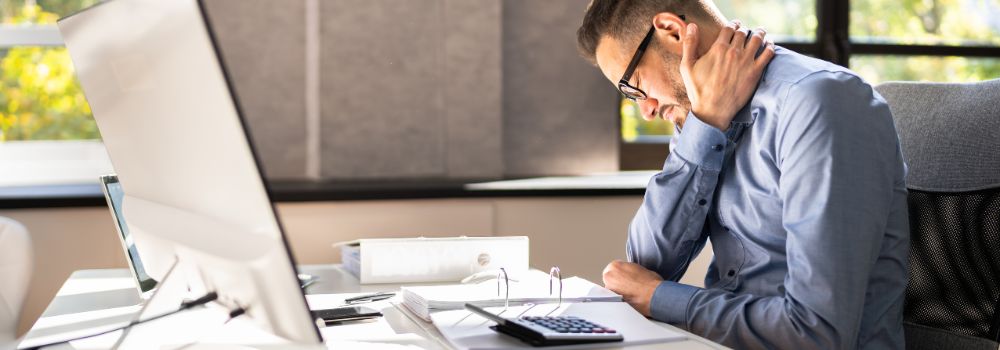
Ergonomic Workstations: Things You Need to Know When Setting One Up
Creating an ergonomic workstation is essential for maintaining employee well-being, increasing productivity, and improving staff retention. Poorly designed workstations can lead to discomfort, musculoskeletal issues, and decreased efficiency. This guide...

How to Protect Your Hardwood Floors Using Entrance Mats
Hardwood floors add warmth and elegance to any home, but keeping them looking pristine requires careful maintenance. One of the biggest threats to hardwood flooring is the dirt and grime...
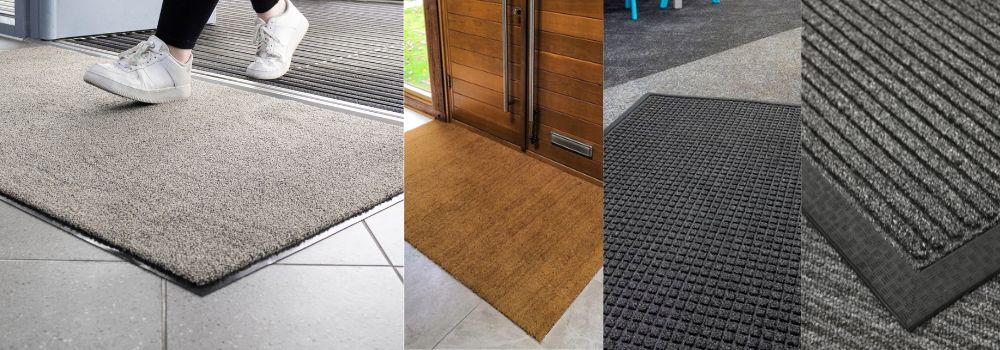
The Different Textures of Entrance Matting and Their Benefits
Entrance mats may seem like a simple addition to your home or business, but not all mats are the same. A mat's texture is crucial in how well it...

What Vegans Need to Know About Door Mats
This article has been written by our Director, Richard O’Connor, who has been exploring how well door mats can align with vegan values. As a vegetarian making more vegan choices...
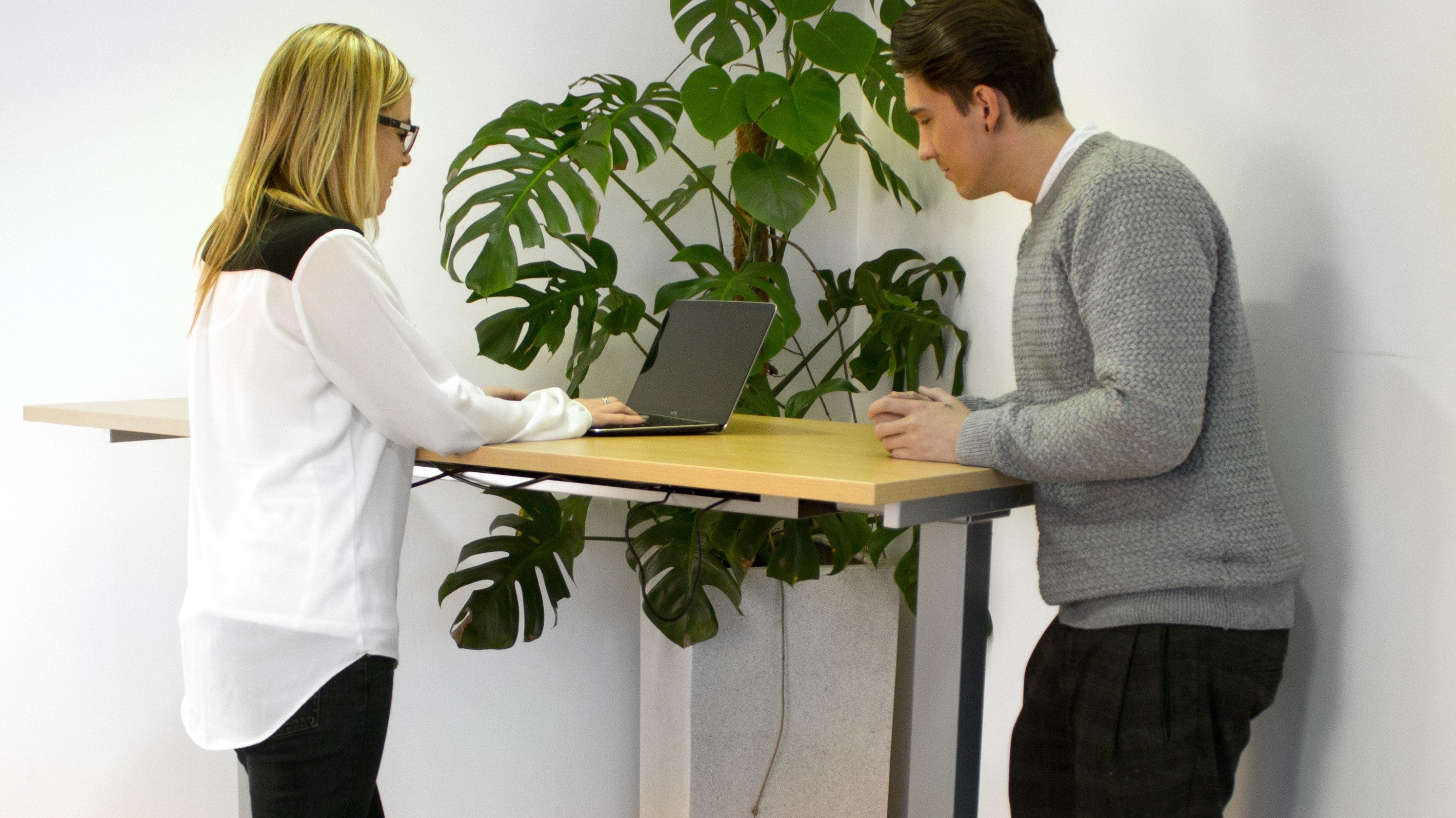
6 Tips for using a Standing Desk Correctly
As people are becoming more aware of their fitness levels and ways in which they can stay healthy, standing desks have increased in popularity because those who have previously had...

5 Creative Ways to Use Your Logo on Products to Boost Brand Awareness
Businesses today compete for attention across countless platforms. Customers have more choices than ever, so brand loyalty is becoming harder to secure. In this landscape, a brand’s image needs to...

The Different Surfaces of Anti-Fatigue Matting Explained
Understanding the different surface textures of anti-fatigue matting is essential for selecting the right one for your workspace. Anti-fatigue mats come in various textures, each designed to provide specific benefits...

Industrial Matting Fact Sheet
Introduction Industrial matting plays a crucial role in maintaining safety, comfort, and efficiency in various work environments. This fact sheet provides essential information about the different types of industrial mats,...

How to keep warm at work: Cost-effective ways to beat the bills
Are you concerned about your business running costs now that energy prices have gone through the roof? Electricity prices have increased 74% for large industrial units in the past...

The Cost of Slips, Trips, and Falls to British Industry
The Cost of Slips, Trips, and Falls to British Industry Are slips, trips, and falls costing your business dearly? Is your workforce underperforming? Are you missing expertise on the floor...

4-Day Work Week in the UK - Key Facts & Statistics
The world of work has seen a lot of change since the beginning of the 2020s, and — in turn — many companies have placed employee well-being at the top...
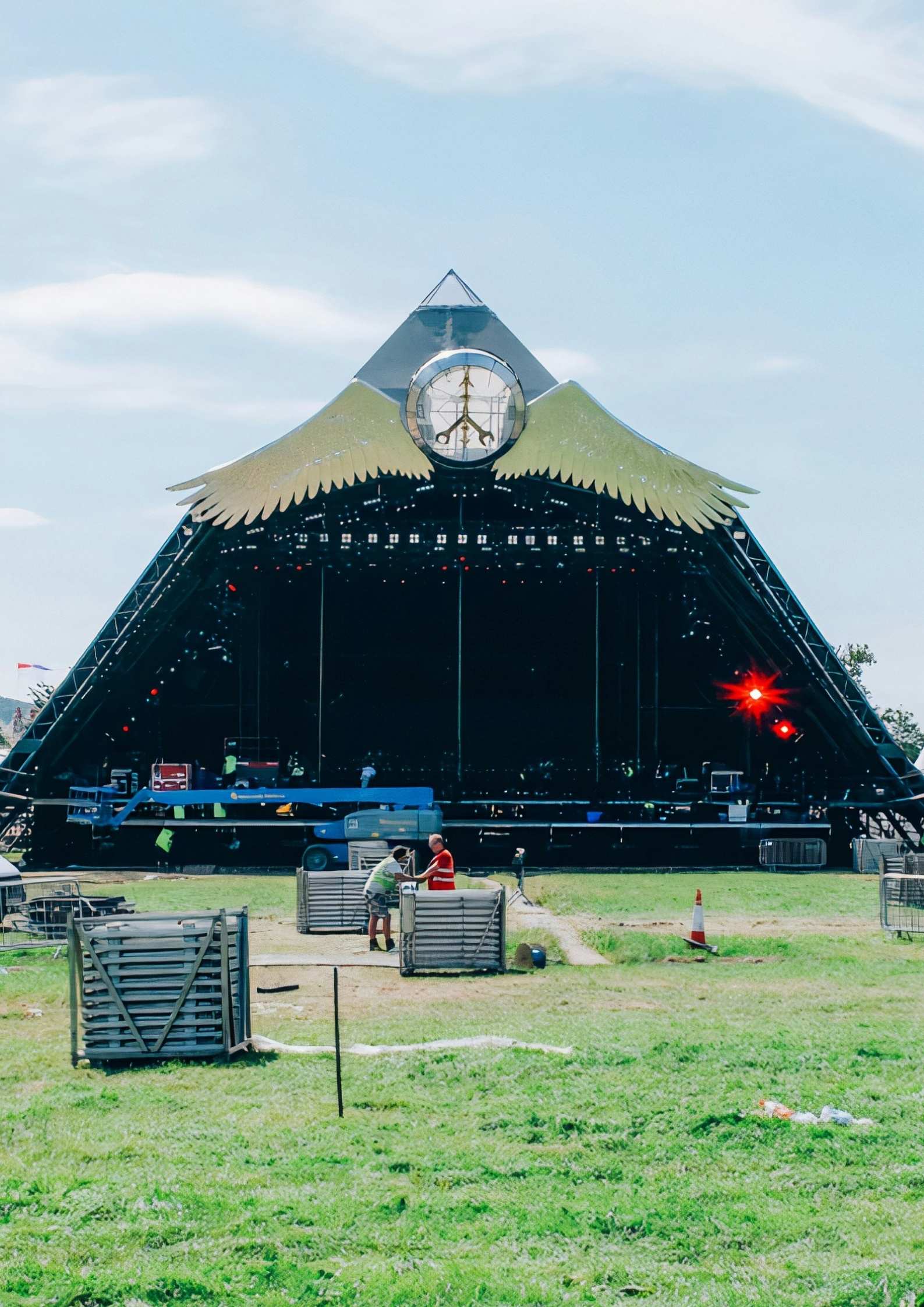
IBC Bunds: Delivered Fast for Glastonbury 2025 Event
Problem Emily Allman from Glastonbury Festivals reached out to First Mats with an urgent requirement for several Double IBC Bund Pallets with Removable...
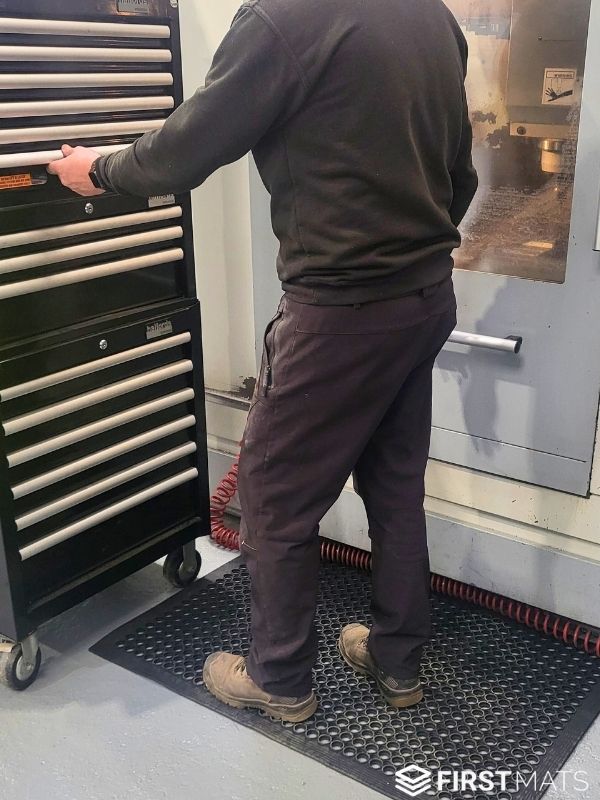
How Anti-Fatigue Mats Are Boosting Operator Comfort and Safety
Problem At Revolution Milling, workshop safety and staff comfort are top priorities, especially in high-use areas like those around the CNC machines. Machine...

Profile Developments: Improving Safety and Style at the Office Entrance
Problem Mark noticed an ongoing issue at the main entrance to Profile Developments’ office. With a high volume of daily foot traffic, especially...

Golden Sands Holiday Park Enhances Safety and Comfort in Pool Changing Areas
Problem Darren, from Golden Sands Holiday Park, reached out following a refurbishment of the site's swimming pool and changing room facilities. Although non-slip...
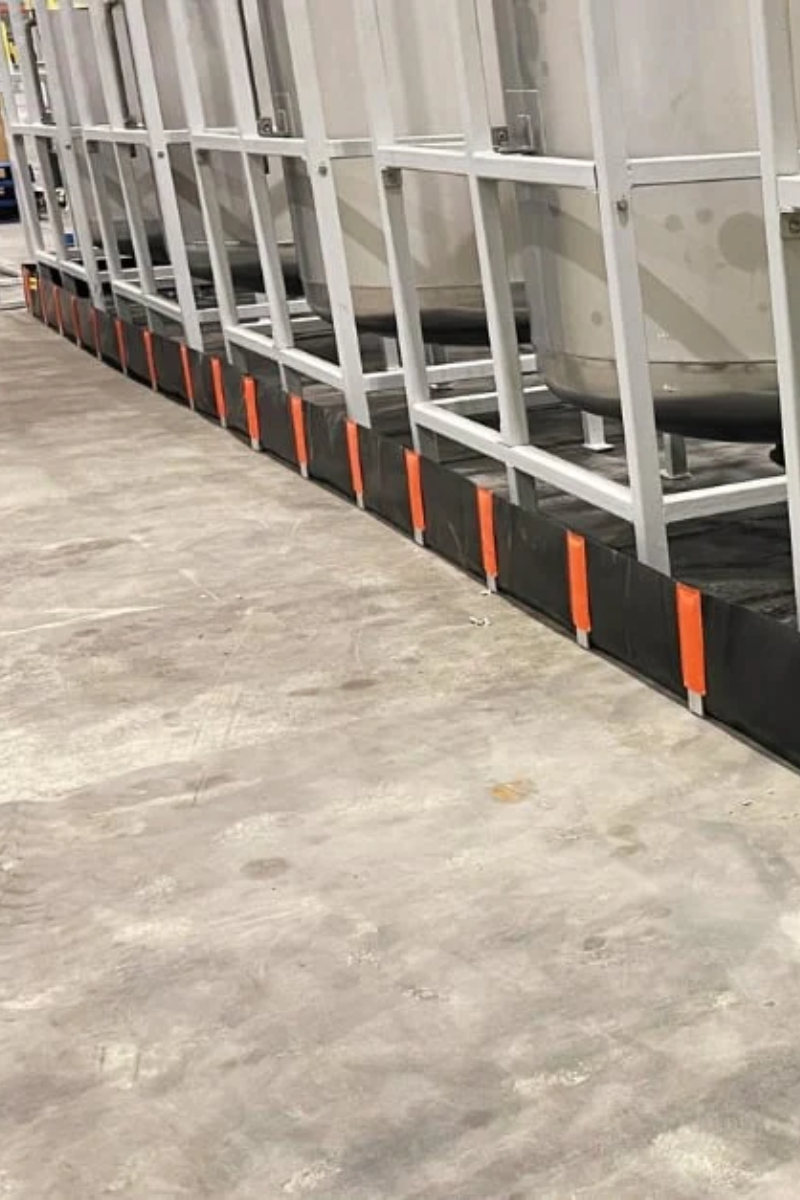
Portable Bunding for Northern Industrial Battery Services
Problem Gareth, representing Northern Industrial Battery Services Ltd, faced a complex challenge during their company relocation. He required a reliable...

Broccoli Cafe Enhances Entrance with Custom Logo Mat
Problem Broccoli Cafe, a stylish establishment in London, sought to enhance its main entrance with a mat that not only fit the unique...
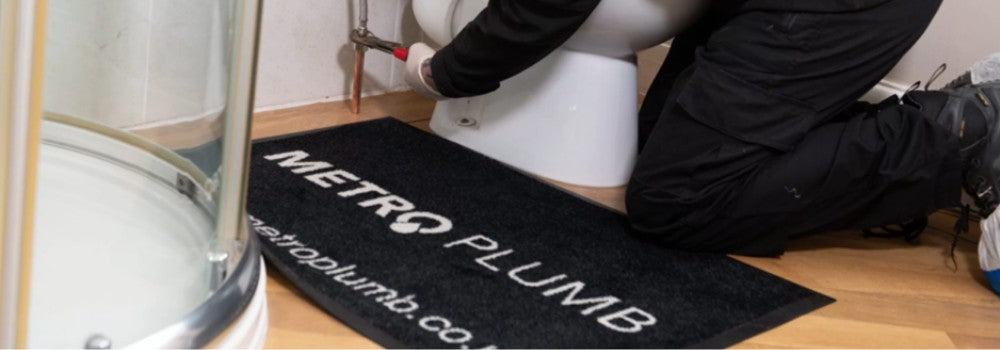
How We Designed and Delivered 300 Logo Mats to Metro Plumb
The Challenge Metro Plumb, a prominent plumbing services provider, sought to enhance its brand visibility and improve the working conditions of its plumbing team using
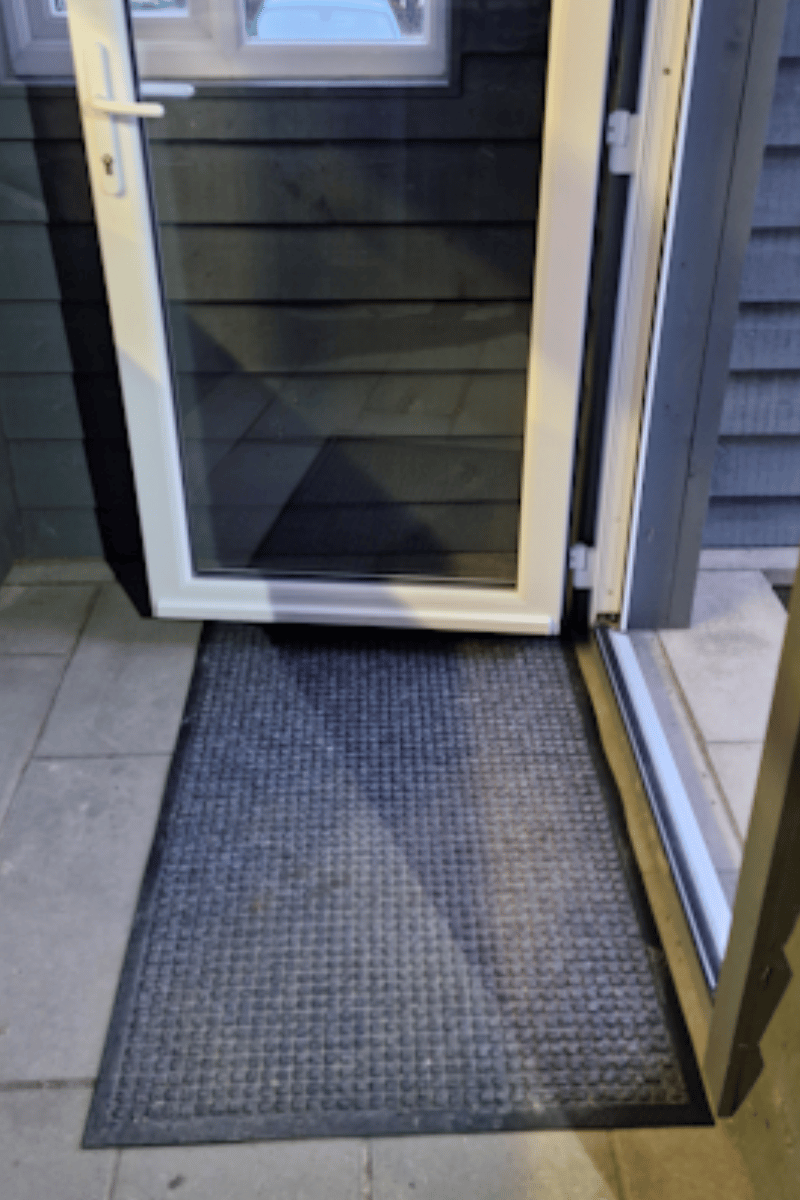
St George's School Achieves Cleaner, Safer Entrances
Problem John, the Site Facilities Manager at St George’s School, faced ongoing challenges with dirt and debris being consistently tracked...
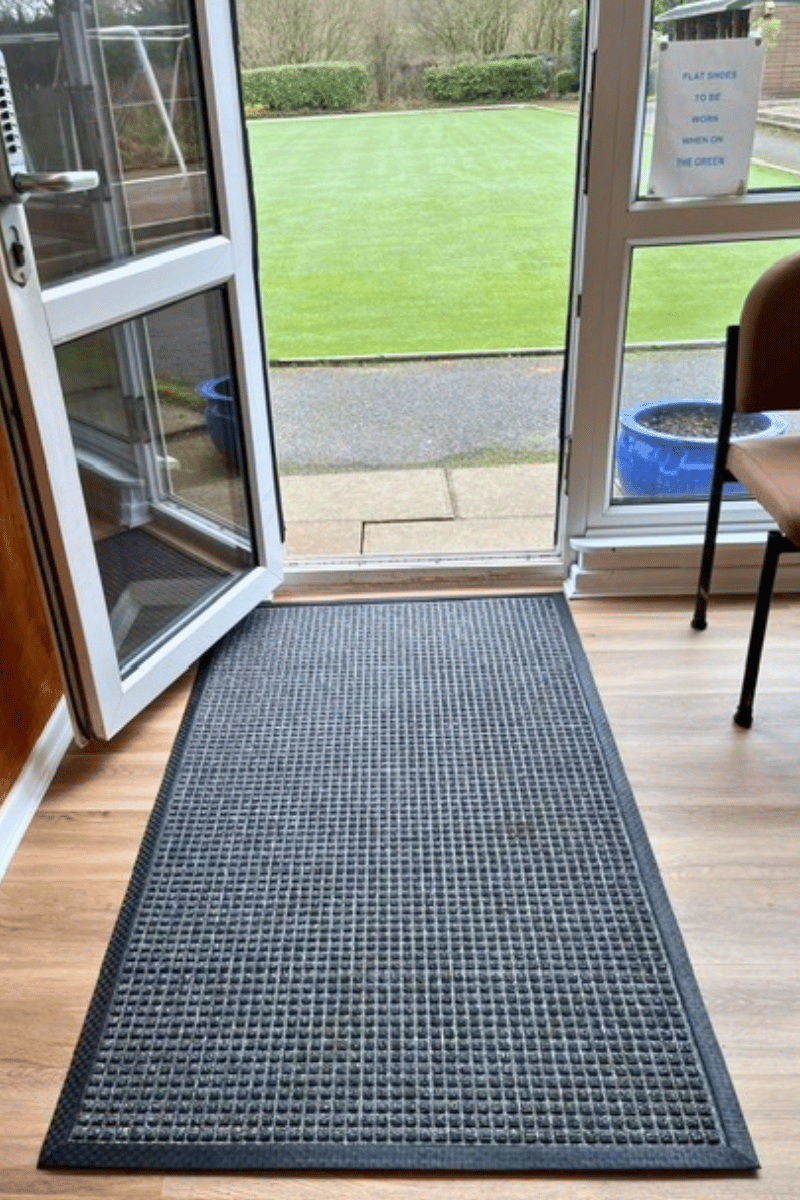
Prestbury Bowling Club Upgrade
Problem When Christine was tasked with refurbishing Prestbury Bowling Club, her primary goal was maintaining a safe, welcoming environment, especially...
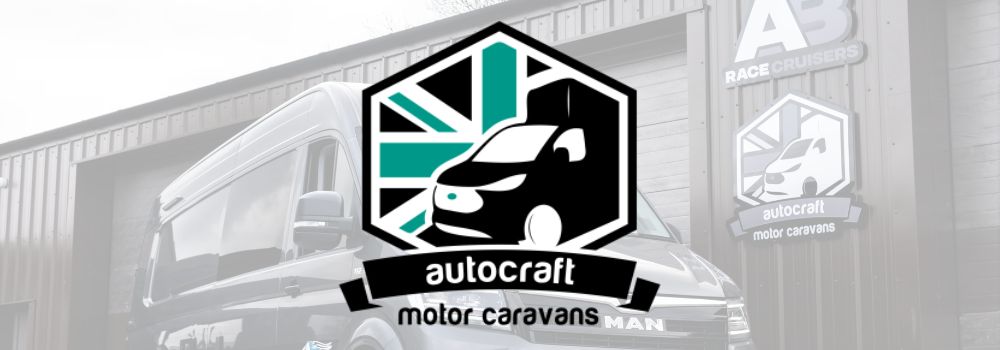
Precision Under Pressure: Crafting Premium Logo Mats for AutoCraft's Big Event
The Problem AutoCraft Motor Caravans, known for their bespoke motor caravan conversions, was gearing up for a significant appearance at the Yorkshire Motorhome and Campervan...
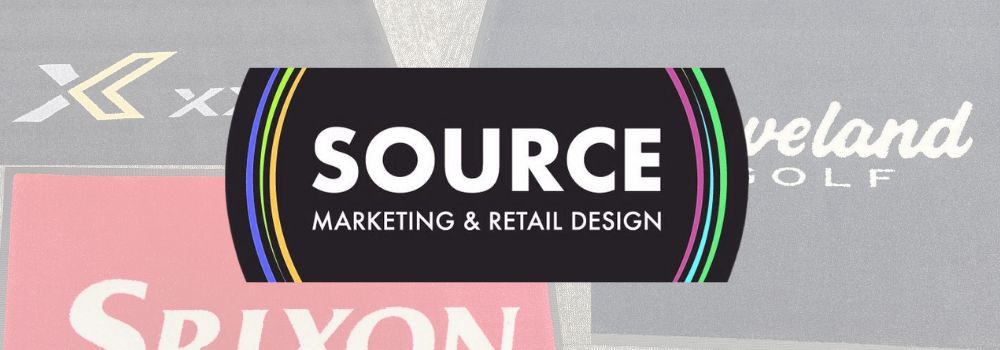
Rapid Response: How First Mats Delivered 524 Premium Logo Mats on Time
The Problem In the competitive world of marketing and retail, visual impact is everything. Source Marketing and Retail, a trade customer and firm specialising...
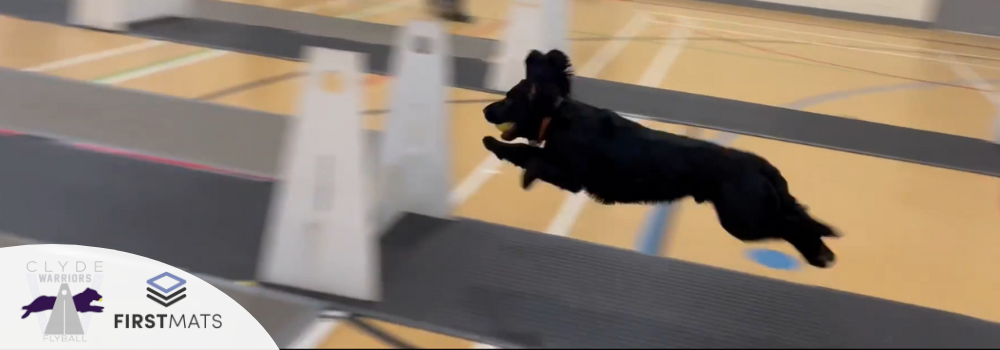
First Mats Supplies Flyball Matting to the Clyde Warriors Flyball Team
The Clyde Warriors Flyball team is a competitive flyball team based in Lanark, Scotland. Flyball is a dog sport in which teams of dogs race against each other over...
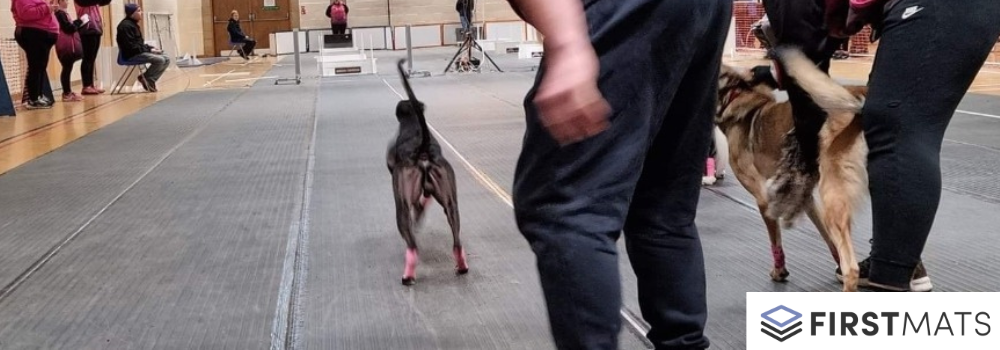
How First Mats Helped Junkyard Dogs with Their Flyball Competition
If you're a dog trainer or Flyball competitor, then you know that having the right matting is essential for providing a safe and comfortable space for your dogs. That's why...
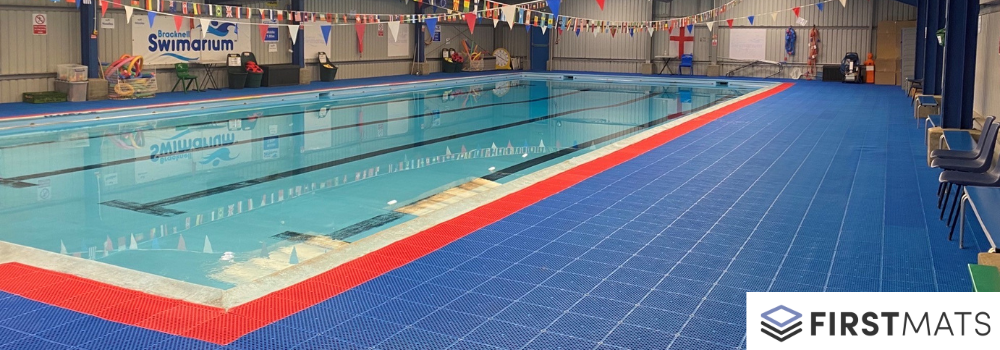
How First Mats Helped Bracknell Swimarium with Their Flooring Refurbishment
Recently, we were approached by Bracknell Swimarium, who required a large amount of our Aqua-Deck PVC Wet Room Mat Tiles for their pool area. However, they needed the tiles fast—in less...
Frequently Asked Questions
If you have any questions, we’re here to help
How long does delivery take?
Each product comes with a specified lead time for delivery. We'll keep you informed if there are any delays in meeting this timeline.
Typically, once you’ve finalised your order and approved the proof, it will take 4-5 business days to make and deliver your finished mat.
If my order is damaged, can I return or exchange it?
Got a problem with your order? If something's not right or you're not thrilled with the quality, just let us know within 14 days of getting it. Drop us a line, and we'll tell you what to do next—usually, it starts with you sending us a photo of the issue. Once we check that out, we'll sort you out with a refund or a new item, no fuss.
Can I get my mat delivered more quickly?
Need your item in a hurry? Just Contact us to explore the faster delivery options we might have for you!
If my custom mat is damaged, can I return or exchange it?
Got a problem with your order? If something's not right or you're not thrilled with the quality, just let us know within 14 days of getting it. Drop us a line, and we'll tell you what to do next—usually, it starts with you sending us a photo of the issue. Once we check that out, we'll sort you out with a refund or a new item, no fuss.